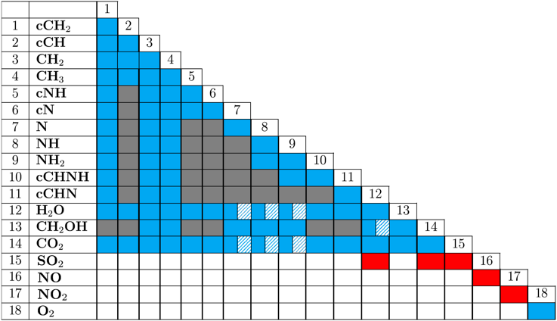
EQUILIBRIUM, KINETIC AND CORROSION TESTING WITH THE ADVANCED APBS - CDRMAX SOLVENT
Activities
Experimental measurements of the CO2 solubility in APBS-CDRMax®, under the influence of flue gas compositions that have high concentrations of sulphur and nitrogen oxides.
Characterisation of the solvent after it was subjected to aging for up to 30 days and at temperatures up to 120oC, under the influence of oxides and air and in the presence of stainless steel specimens. Properties that were measured included amine loss, viscosity, density and metal ions in the liquid.
Inspection of the metal specimens under electron microscopy and energy dispersive X-ray spectroscopy (SEM – EDS) for evidence of corrosion and deposition of degradation products. The study also employed a range of electrochemical techniques, including Open Circuit Potential measurements (OCP), Potentiodynamic and Cyclic Polarisation curves, and Electrochemical Impedance Spectroscopy (EIS), to provide insights into the corrosion behaviour.
A model has been developed based on the SAFT-γ Mie equation of state regarding the inclusion of sulphur and nitrogen oxides in mixtures of CO2 amine and water.
Apparent solvent kinetic measurements were performed to provide data for solvent modelling.
Key results
The APBS-CDRMax® solvent exhibited much higher capture capacity and 20 times better corrosion performance than reference solvent monoethanolamine (MEA).
It also exhibited high resilience in the presence of a large concentration of contaminants such as sulphur and nitrogen oxides.
A general model and parameters have been developed for the prediction of phase and chemical equilibria in CO2 capture systems that may account for the presence of sulphur and nitrogen oxide species. This has enormous practical value, as it is possible to derive predictions for realistic flue gas compositions. The model is based on SAFT-γ Mie equation of state that, by design, may be applied to a wide range of settings, including CO2 capture from industrial effluents, but also in the context of direct air capture or capture from natural streams. The model is highly transferable to other industries, e.g. pharmaceuticals or agrochemicals. The parameters can be used through both commercial (gPROMS) and open source (Clapeyron.jl) software.
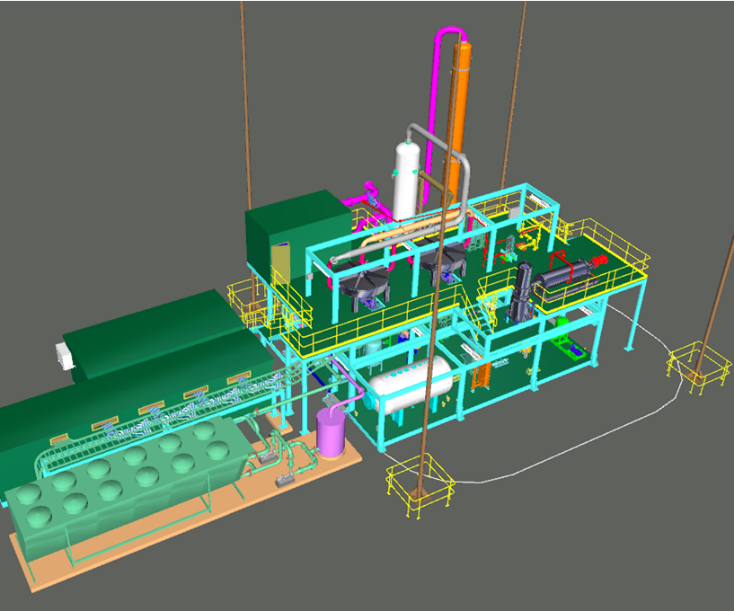
DESIGN AND CONSTRUCTION OF PILOT PLANT
Activities
Significant preparatory work has been undertaken with respect to the design and construction of the capture plant.
HAZOP, HAZID and ATEX analysis took place to determine any necessary improvements that ensure the delivery of a safe plant that is acceptable for use.
The work included the development of 3D layouts of the plant and its virtual placement and connection to the host sites.
Key results
Safety assessments have been conducted that resulted in a safe capture plant that is acceptable for use by the industrial host sites, while the detailed 3D design has indicated the very low plant footprint.
The process flowsheet includes a two-stage RPB absorber and RPB desorber with Integrated Stripper and Reboiler (ISR).
The RPB absorber enables interstage cooling which improves CO2 capture efficiency, reduces regeneration energy and helps lower solvent degradation and emissions.
In the RPB-ISR the temperature difference between the solvent and the steam used to heat it can be lower because there is no requirement to generate vapour at pressure, allowing improved heat transfer. Furthermore, heat loss from the walls of the single RPB-ISR is reduced compared to if there were two separate units. Both these factors act to reduce the energy consumption compared to an RPB desorber with an external reboiler.
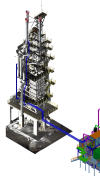
DEMONSTRATION OF ADVANCED RPB CAPTURE PLANT AT 3 INDUSTRIAL SITES IN EUROPE (QUICKLIME, POWER GENERATION, REFINERY)
The capture plant will be installed and tested in a quicklime production plant, a natural gas-fired power plant and an industrial gas boiler.
The sites have performed preparatory work pertaining to positioning, connecting and permitting of the capture plant.
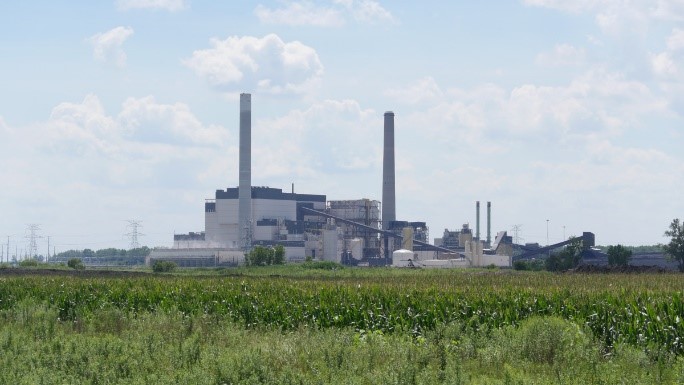
PERFORM SCALE-UP, UTILIZATION AND SEQUESTRATION STUDIES CONSIDERING AN INDUSTRIAL CLUSTER
Activities
A framework for the LCA has been developed, considering data regarding solvent degradation products and models for solvent reclaiming.
A process model considering integrated RPB-based absorption/desorption has been developed and validated.
Key results
The developed RPB-based process model has exhibited an excellent match with experimental data, as it showed a 2.2-4% average deviation in indicators like lean loading, reboiler duty, absorber CO2 gas fraction and liquid temperature.
Regarding the LCA data, potential degradation products were singled out. The LCA framework for the process has been delineated individuating the inventories (i.e. foreground data) required for the cradle-to-gate part of the environmental sustainability assessment. A solvent purge reclamation and recycling system was conceptualised including an estimate of the materials and energy balances for the LCIs.
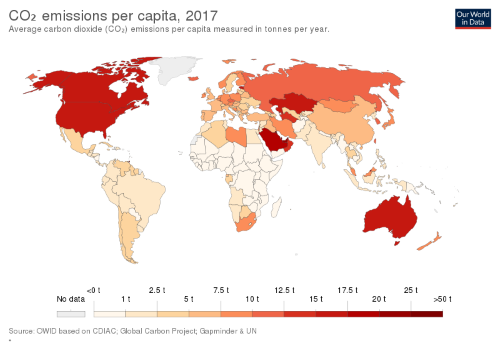
PERFORM SOCIETAL STUDIES AND POLICY ASSESSMENT TO INVESTIGATE THE EFFECTS OF THE DEVELOPED TECHNOLOGIES ON SOCIETY
Data regarding societal stakeholders have been gathered and the details regarding their engagement through interviews and focus groups have been determined.
We have developed measures including a questionnaire to assess several variables (e.g. previous knowledge of CCUS, risk and benefit perceptions etc.) and interview protocols. We have identified focus groups including university students and local residents, industrial stakeholders, local government officials and media people.
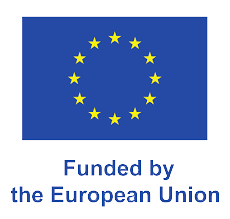